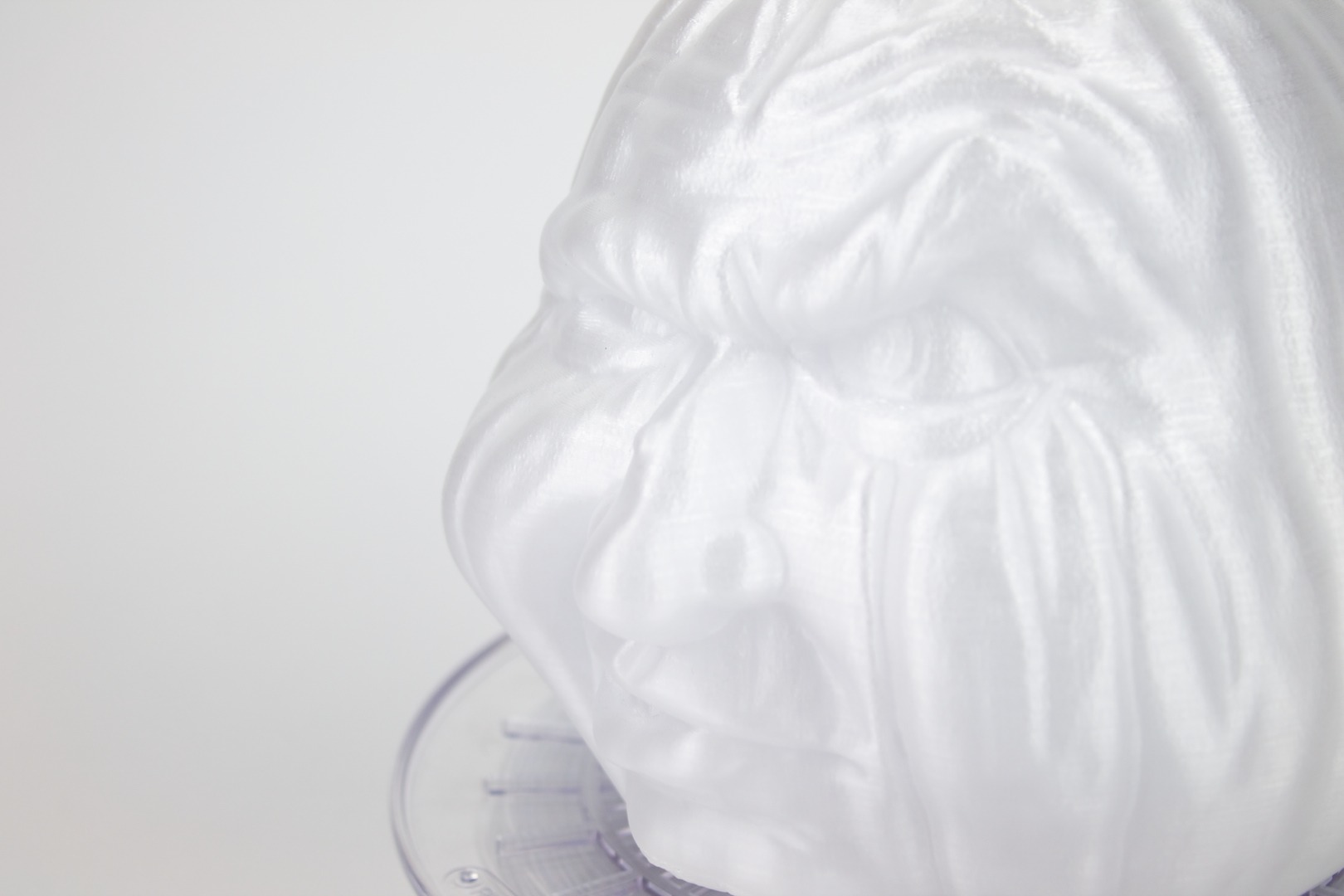
Our _XT filament has been around for a while now and we’ve been getting lots of positive feedback and tips. Therefore we decided it was about time to do a little write up of all the tips and comments to help you get the best possible quality from your 3d printer.
One of the unique aspects of the XT-Copolyester is the melt strength. This is what makes for good bridging properties and toughness of the overall material. But it also means higher temperatures are needed to reach the appropriate viscosity which is needed for printing at various speed settings.
Ultimaker 2 – speed and temperature settings
[table id=3 /]Retraction settings remained unchanged, 40 mm/s speed and 4.5 mm distance.
Ultimaker Original – speed and temperature settings
[table id=4 /]Retraction settings remained unchanged, 40 mm/s speed and 4.5 mm distance.
Heated build plate
_XT is best printed with a heated build plate. The ultimaker 2 uses a glass plate which we cover with glue stick. We keep the build plate at around 70C because this material also features a higher glass temperature of about 75C. This means your prints will be able to withstand heat better then for instance PLA prints.
Cold build plate
If you don’t have a heated bed and you do want to give XT a try then we advice the following. Print on blue painters tape and make sure the build plate is perfectly level and the distance of the nozzle tip to the platform is spot on for the first layer. Then the trick to minimize warping on a cold bed is to disable the cooling fan for the first 1-2cm. If your part needs cooling you can switch it on after having printen a few cm high, if you don’t need it just leave it off. Because your not cooling the material to aggressively it won’t warp as much. You should be able to print on a cold bed like this, but do expect some warping. Additional measure can be taken to minimize warping by enabling either ‘brim’ or ‘raft’ settings in you slicer software.
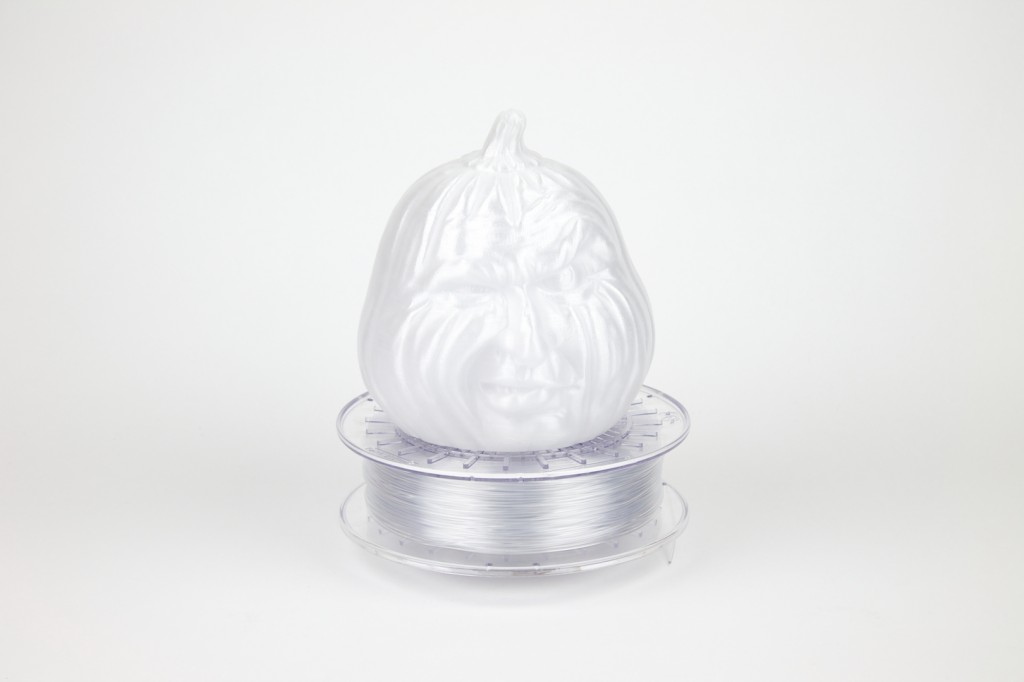
Transparency
To get the most transparency out of the print you could try the following:
- disable cooling fan for the entire print
- print slowly, 20-40 mm/s
- increase flow rate, so the perimeters melt together
- print at rougher layer heights, such as 0.27mm – 0.35mm
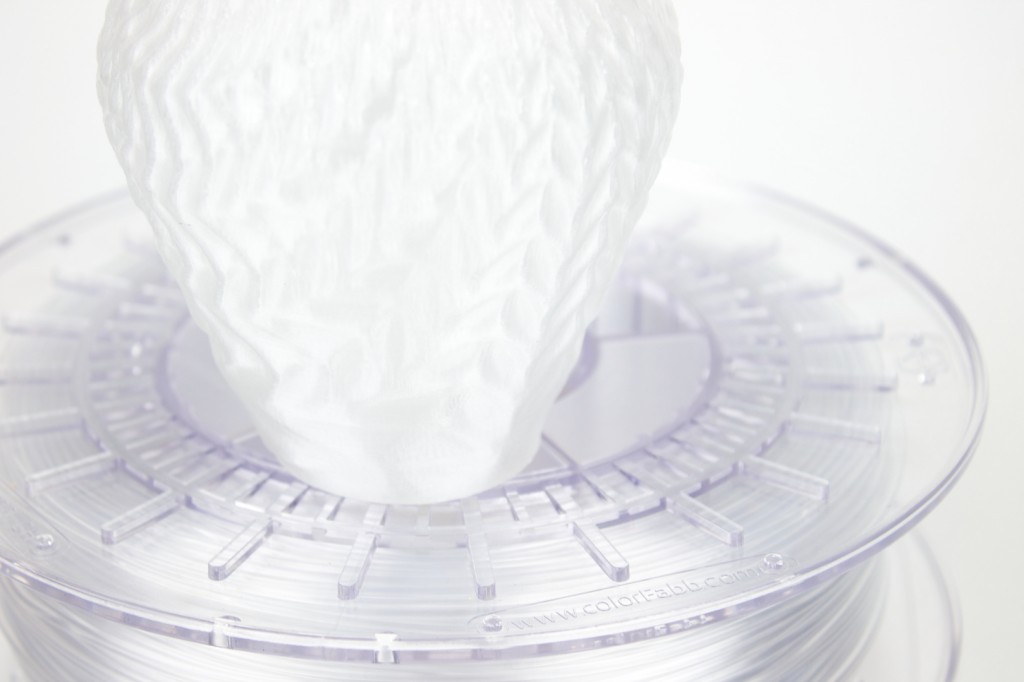
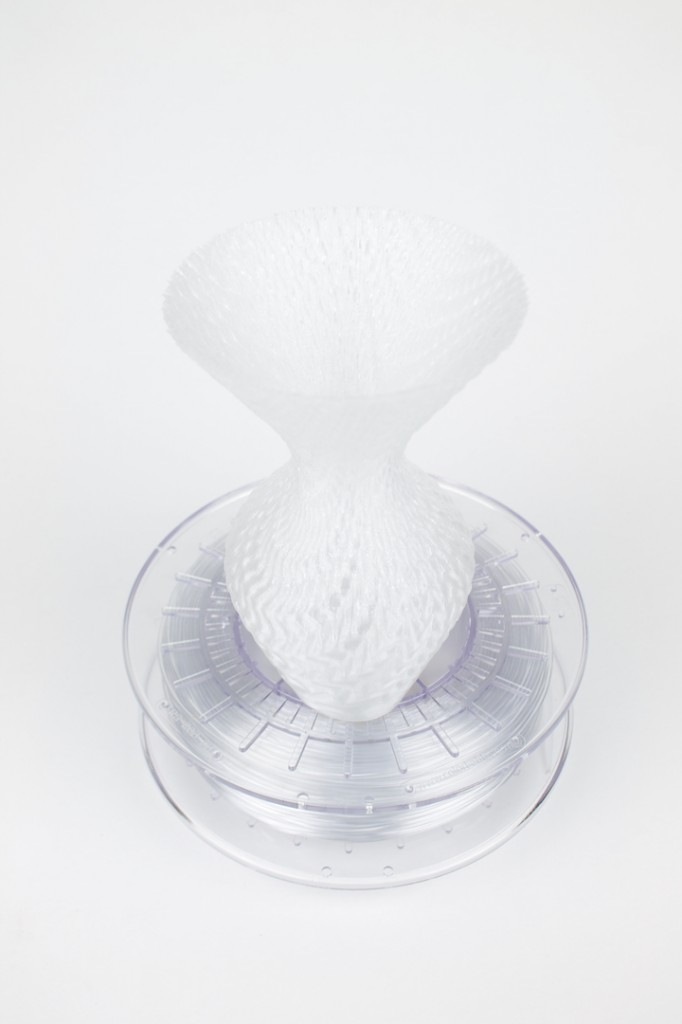
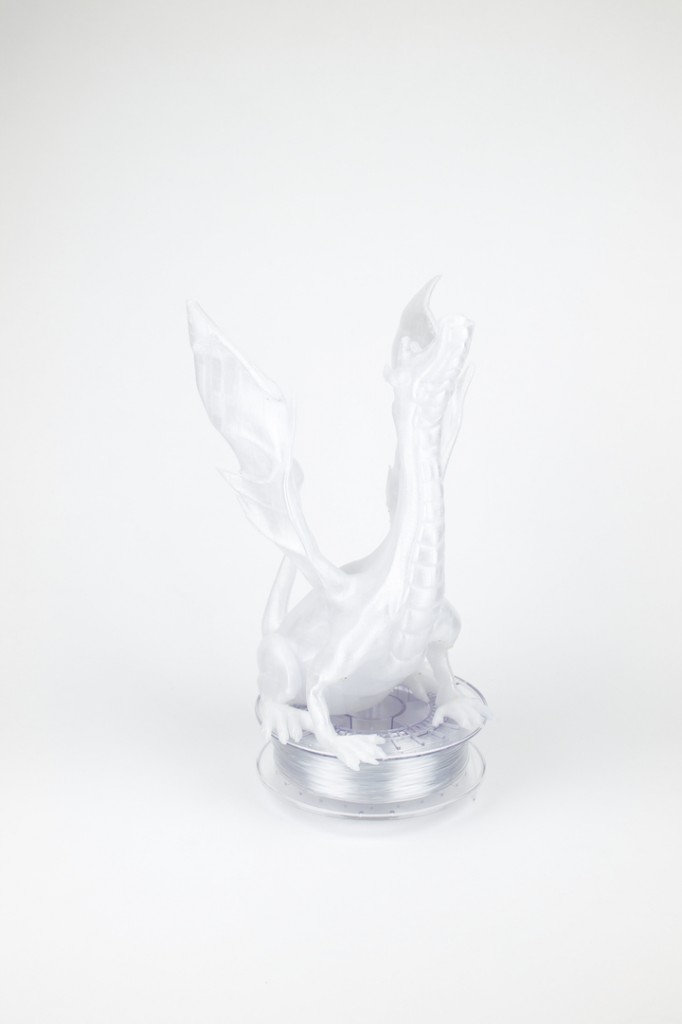
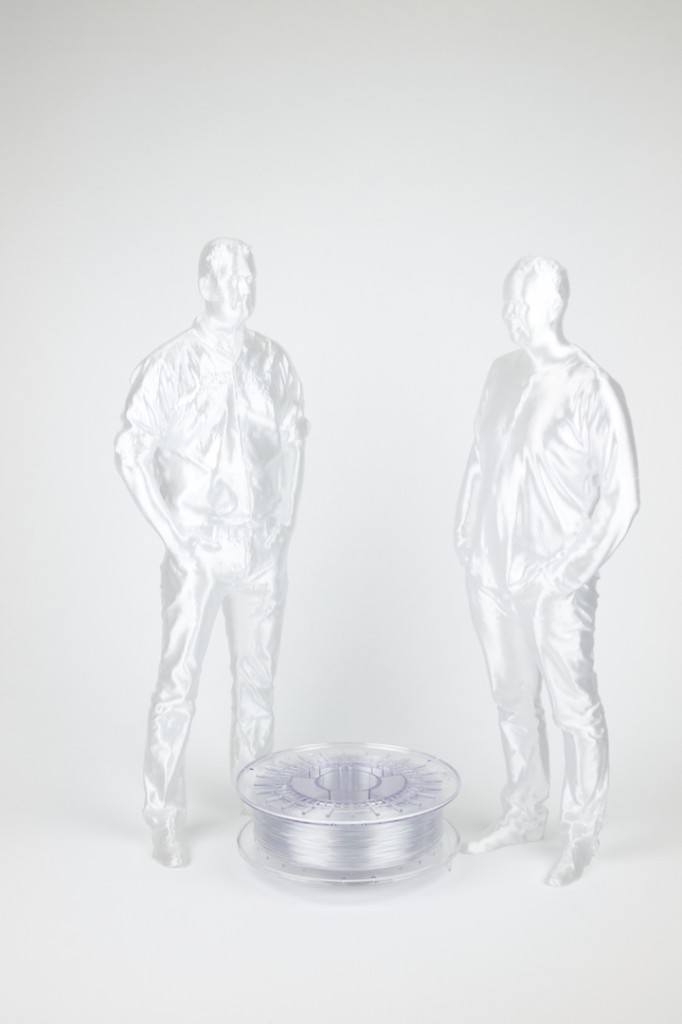
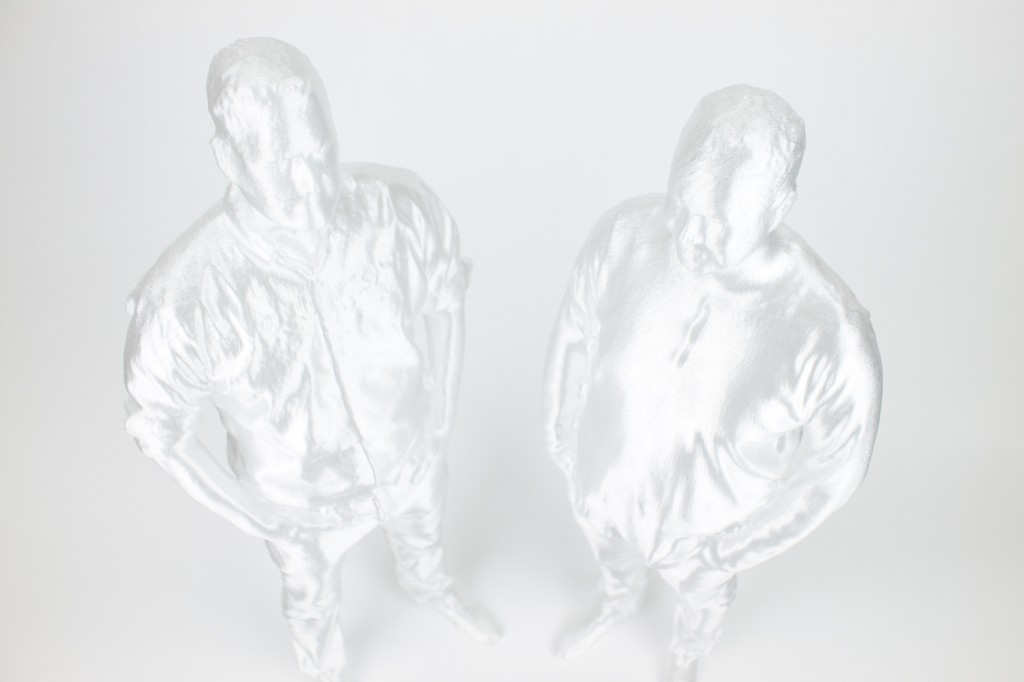
[mwi_product sku=”020011″/]
87 Comments
Do anyone have info for a MakerBot replicator mini+ with the experimental extruder? Can it even be used on this printer? I have been playing with different setting but I have not been able to get a good start on the base.
I have tried various temperature, speed setting with no luck.
Hi
I use colorfabb_XT-CF20 and most of the time I get rely good results. I think this product is amazing, I do however need some help,I’m getting a build up of material on the nozzle, which some times get hard enough to catch on the print which causes the X or Y axis to jump on the belt and of course ruins the piece could you let me know what might be causing this.
Colorfabb support, major respect for handling some aggressive and foolish customer comments with grace.
I do have an issue I need help with. I’m printing in clear HT, as well as XT, and I keep experiencing otherwise-perfect large (200×250) prints ruined by a few burned particles embedded in the print. For the colored versions of the filament it’s not a big deal as it would usually be obscured by the opaque shell, since it typically falls into the infill. I’m trying to print the Makerbot headphone stand and sand it down to get that glass-like finish on the outside, to better show the infill (hopefully).
The problem is worse when print speed is slower (20mm/s vs. 40mm/s) and the particles seem to appear during roof layer printing. I’ve cleaned my nozzle with a wire brush and the channel has been flushed with more than a full spool of XT at present.
This can be caused by a slight blob of material slowly collecting on the nozzle which when big enough falls down in to the print.
As you mention it occurs mostly during roofing, take a look at how those first layers are seated on top of the infill.
Maybe these curl up too much or otherwise get snagged on the nozzle?
To me this is the best filament i have printed with, super strong and good looking prints. I print a bit hotter than quoted 255 and 85 but this may be something to do with types of printers. layer 1 no fan, layer 2 50% fan and 100% from layer 3.
I make actual usable parts for industry with this stuff. Good Stuff.
One Massive piece of advice, just because the firmware says the bed is 80 degrees that doesn’t mean the top of your glass plate is 80 degrees. It may take another 30minutes !!!!!! for the glass to get to that temp..
Happy Printing.
Hi
I would like to use this XT-CLEAR with an ULTIMAKER 3. Is that possible? Where can I find the settings?
Best
Mahyar
Hi Mahyar,
A good starting point would be the default CPE profile in CURA.
The problem I see with this XT comment section is that you keep diverting people to email and we never see the results. Is there a place where we can see if they were ever successful? Do you ever update this article with any new settings for these printers as you (hopefully) solve everyone’s issues?
I would love to find a place on your websites where you list all the settings for all your materials for the printers you know that have successful prints. Even just for the printes you actually have in your shop. All in one place – that would be a wonderful resource! Do you have one?
Updating the articles is something we are working on. In the meantime, we regularly post prints with various materials on the printers we have in our print lab – colorFabb_XT being one of them. We post the settings we used in those articles. Thanks for the suggestion!
Do you hace any recommendations or settings for Xt copolyester in a prusa MK3? Im using a texturized steel sheet and it does not adhere 🙁
2017 June, Bought a couple rolls of white XT and attempt to print objects for a couple of days now.
All prints fail on the infill. Tried with and without fan, temperatures from 240-250 C, toggled retraction etc. Even when setting the infill speed at 20mm/sec. Behavior is the same when using Cura or Slic3r.
Printing objects without infills goes however smooth.
We do print a lot here since 2013. With ABS, Flex, PLA etc. Never seen any material behaving spooky as colorfabb XT.
This material should not be sold to the public.
Hi Bob, sorry to read that you have problems with our filament. I will forward this to our technical support to follow up. colorFabb_XT was succesfully launched almost 3 years ago and has found a lot of fans among engineers and prototyping professionals looking for a functional material. I am sure our technical support can help you further.
Works ace for me, currently on a roll of XT in Blue thats so good, its pretty much ended my days with PLA entirely – great work ColorFabb!
Update: After having received a support email from Gijs, we decided give XT some more tries and bought the latest factory-build Prusa i3 MK2S for this purpose.
Good! In combination with the Prusa Slic3r, colorfabb XT prints now near perfect.
Working settings:
-print-speed: 40mm/s, first layer speed: 15mm/s
-nozzle: first layer 250C, other layers 247
-heat bed 1.st layer 80, other layers 65
-fan off for first 3 layers, then gentle between 25% up to 40%
-Infill line-with: 0.4 mm
-infill/perimeters overlap: 50%
-layer height:.15mm
We printed 12 cm high objects with minimal warp (.2mm on the longest edge).
XT sticks very well on theadheses MK42 heat-bed.
Thank you Gijs!
We got the quite same conclusion here on our MK2S:
-first layer speed: 15mm/s
-nozzle: first layer 240C, other layers 250
-heat bed 1.st layer 90 (we noticed a better adhesion with 90C than at 70C like in the Prusa preset), other layers 70
-fan: 10% to 50%
We got stuck long time with the poor adhesion but a very slow speed is the key.
Else may differ on what you print. With Linear Advance activated and flow limited to 10mm3/s:
-Layer height: 0.25 (to easily reach 10mm3/s without having to go up to 100mm/s)
-First layer height: 0.20
Widths:
-First Layer: 0.5
-Perimeters: 0.45
-External perimeters: 0.6
-Infill: 0.55
-Solid infill: 0.5
-Top solid infill: 0.5
Support material: 0.5
Overlaps: 25%
Speeds (limited by flow max):
Perimeters: 100
Small perimeters: 100
External perimeters: 45
Infill: 100
Solid infill: 100
Top solid infill: 30
Support material: 100
Bridges: 30
Gap fill: 60
Work on parameters still in progress.
Is there a way to import these settings to cura?
i thing its good material…u only need to find good settings and it will print
I’m surprise to see so many negative comments. I think that the huge majority of people with a bad feedback just don’t set their printers right. It can be challenging to fine tune your printer relative to the shape of your print and the material but a failed print doesn’t mean that the material is crap. I think XT is a very good filament. I’ve been using it intensively for the past 2 and half year.
So I just want to thanks Colorfabb for the quality of their products.
Printed two objects now, and am still calibrating the slicer settings for the XT. Like that I don’t have to be so afraid of BPA contamination while printing this. I got the heat and bed heating settings correct, and it is now printing quite consistently. Thanks for the great product, ColorFabb.
I must second the problem list. I spent the last two days trying to get a usable setting for XT white on a UM2 with e3d v6 hotend. Simply not possible. None of my calibration objects finished with acceptable quality. I tend to get underextrusions on nearly every print. I tried w and w/ retraction, temp range from 240-265 °C the only thing working is the stick to the buildplate and the neutral smell.
worst material I’ve tried so far.
We’re not sure about the UM2 combined with E3Dv6, but both the UM2 and E3Dv6 (on our Delta Tower) have no problems printing _XT in our labs.
Let’s get in touch via support@colorfabb.com so we can judge what’s going on here.
Depending on the slicer you’re using, make sure you’re not printing wider than the nozzle size (extrusion width).
Temperatures for the E3Dv6 are on the higher side, running 260 – 265c on the 2,85mm variant.
You could even try it a bit higher, if you go too high in temperature you’ll see as the material will start to bubble and pop.
Do you offer refunds? This is the first time I cried because a filament disaster!!!!
Hi Erman,
Contact us with the details on support@colorfabb.com and we’ll take a look at the request.
If there’s a material issue we will certainly compensate.
Please also send your printer info’s and slicer settings so we can get a good understanding of what’s happening.
Worst crabby material I ever used. If you look in the internet allmost every user got major problems with XT. Me too.
I’m very angry about this crab XT material and your published settings (Ultimaker Original). I took it one by one and after 1 cm (cooling fan started) the printer started to print crab. All the fine details and the support structures started to delaminate and the print temperature was 245°C! Filament was XT light green.
We’re not sure what you mean by “crabby” material Tom, could you clarify?
Keep in mind that keeping the fan off if not needed is advised. Especially since the UMO has quite a powerfull cooling fan.
Delamination is most often by a lack of heat to fuse the material together. Too much cooling or not enough printhead temperature are your main suspects.
For more detailed advice please send us some more details (slicer settings, pictures, gcode) to support@colorfabb.com so we can take a closer look.
Jos, I’m sorry to say this: with this material for me it isn’t possible to get any acceptable results. I tried different printers (Malyan M150 and M180) and different settings. With this printers I’m able to print complex objects with PLA, ABS and TPA. Why not with XT?
If I print flat structures or simple objects everything fine, but thin objects with shell characteristics I got major problems. I tried it over and over. Only results: I wasted money (1 spool red and 1 light green) and time.
My latest experiments were with higher temperatures (>255°C, fan off, enclosure, raft). Nearly same results, the oject came up (warping), the hot end ran against and everything was out of adjustment.
I will send you everything you requested.
I just can’t get this material to print anything. Super disappointed – thought it said that it was pretty easy to use??
Hi Luke,
please contact us at support@colorfabb.com and we will take a look at your issues to see if we can help.
If you can include some pictures and the gcode and slicer settings used we can get the best idea of what is going on.
Bonjour à vous.
Malgré de nombreux essais, avec mon imprimante XYZ Printing PRO, je n’arrive pas à imprimer convenablement.
Avec l’XT, il n’est nullement transparent et est tout grumeleux.
Avec le noir et le bois, la tête se bouche dans l’imprimante après dix minutes d’impression. Galère pour tout retirer.
J’ai testé avec la prusa où je peux faire les réglages durant l’impression… rien ne va.
J’ai testé avec les réglages recommandés et avec mes réglages à moi. Rien n’y fait. Avec ou sans ventilateur, de 220° à 260°, vitesse lente ou rapide.
J’ai quatre bobines que je viens de mettre à la poubelle.
J’ai cinq autres marques et toutes fonctionnent.
Bonne continuation.
Bien à vous.
I’m sorry but we do not have a French speaking colleague.
But as I understand from Google translate you are having troubles printing with some material?
Please contact support@colorfabb.com (in English) with as much details, settings and pictures as possible so we can try and figure out how we can help.
Problems here with my ormerod2 and coloured XT. I am using slic3r . I tried with temps from 240 to 260, speeds between 35m and 55mm, with fan off or on, layer 0.15 or 0.2, extrusion set at 1 except for first layer that is set at 120%. My issue is curling on corners (which seems reduced with a cooling fan) and infill breaks apart (with rectilinear fully and honeycomb partly).
Overall, I have not managed to get a single decent print except for cubes or cylinders. And even there the top layers was pretty bad.
Any help would be appreciated.
Hi Francesco,
Please contact us via support@colorfabb.com for specific issues like this.
Via our helpdesk system it’s easier to address specific issues / questions and also to share data like pictures, settings etc.
Please include as much data and visuals so we can get a complete picture of what could be going on here.
Hi,
I have seen mention above and previously about Old and New colourfab XT.
I have a batch labelled April 24 2014. Is this Old or new?
I am struggling to print a very small part with a lot of support. the flat-bottomed parts are sticking well, but the small support fins are getting pulled up again as the nozzle moves around. I will continue to experiment and report back, but if anyone has had any particular experience like this I would appreciate some advice.
I have experimented with upping the temperature slightly, using blue tape as well as elemer’s glue stick (which works great with ABS)
My starting point was 235C / 70C at 50mm/s, then I tried a higher temperature, then I tried a slower speed.
This was the last Print I did in XT for your interest:
http://zaxis3d.uk/?portofolio=rose-in-colorfabb-xt
Thanks,
Greg
Hi Greg,
Only production dates from before February 2014 are the old formulation, so you have the new (current) XT-Copolyester.
That print you’ve shared looks amazing, nice work.
If your still having trouble with the bed adhesion we can try to help if you contact support@colorfabb.com
There we can share some more information and go in to more detail.
Of course you could try a brim to keep the support down and indeed slow down the first layer speed.
Also make sure that your nozzle is not worn down to a point that the flat spot at the bottom (the shoulders) becomes to large.
The easiest though might be to slightly adjust your model in that you include some custom support material in the .stl file.
Thanks for your reply
In the end I printed the model in a different orientation with custom support so the original issue went away, but I think that slowing down the printing of the support fill may have worked- and I will try that , as well as the other suggestions if necessary when time allows.
In fact today I got a new job for XT clear …the customer is looking for something as close to transparent as possible… I read something about a coating that makes it almost completely transparent with a single wall thickness …can’t seem to find that again now.
Here is the result anyway- http://www.thingiverse.com/thing:1162636
Maybe you mean XTC-3D?
We have no experience with these kinds of products and their effect on the XT-Copolyester.
True transparency is pretty much impossible due to the process of 3D printing.
But using a larger layer height and maybe a bit higher temperature will help with transparency.
Also our new nGen will gave a more transparent result we think.
Maybe you should point out that the clear XT and the coloured XT (I have red) are pretty different animals:
* the red one feels waxy, almost like HDPE (or polyamide? maybe I should print a solid bar and see how it machines), but more rigid, needs 250C to stick to the bed (70C, painter’s tape), and is pretty strong, especially when printed with thick walls (I printed some change gears for the lathe last night, they seem to take the effort just fine and are more quiet than the POM originals).
* the clear one feels more like PLA (rigid, brittle but somewhat less so than PLA), prints fine at 240C (same bed temp / cover), and small sections delaminate quite easily (I might have to try printing it hotter, though)
Both have a tendency to generate “snot” on the nozzle at times, but otherwise they print very cleanly and are nice materials overall.
Hi m0n5t3r,
Both the clear _XT as well as the colored _XT are the same material, aside from the colorant of course.
They are copolyesters, Eastman’s Amphora material.
The clear material should not behave differently than the red and should definitely not be brittle.
Please contact us at support@colorfabb.com with your findings and some pictures of the material so we can investigate.
Hi everybody, I just recived my samples of _XT Filament and will start to print it soon.
I wondered if I need to change the hotend/nozzle of my printer before that to a new one. I printed only with the Colorfabb PLA/PHA before.
I was thinking of jams in the extruder if i alternate between these materials, like it happens with the change between ABS and PLA for some people.
Thanks!
Hi RobotRock,
Hope your tests will be going well.
We never switch hot-ends / nozzles when changing to a different material, so it shouldn’t be necessary.
Usually we heat up the printer and manually push some of the old filament through before pulling it out fast.
This will ensure that most material is out of the nozzle which will make color / material changes faster.
When switching back to PLA/PHA or another lower temperature material, make sure to flush out the XT-copolyester at it’s printing temperature before turning down the heat.
Hi,
I am using the white XT and the XT with carbon fibre, had some issues while printing but getting better every time. My doubt is there is any trick to polish the printed objects in these materials? Thanks 🙂
Hi Silvia,
We have no special tricks for polishing.
Sanding is possible but as with most plastics it takes time.
Still waiting to hear back from support@colorfabb.com
Still waiting for a decent print! lol.
This material is a complete 180 from the old CoPolyester, which was the best material I have ever printed with.
The new COLORFABB_XT is by far the WORST material I have ever used.
-Alex Petrov
Hi Alex,
The ‘new’ XT-Copolyster has been the standard for a long time now.
We will continue to work with you at colorFabb support to diagnose the issue because this is something we never experience.
The improved melt strength is a good upgrade for technical parts, but it does mean you need a higher printing temperature.
Please continue to investigate this issue with us,
Jos.
———- Edit: I’ve added your updates below, Jos. ———-
Got a few problems with mine. I got some of the pink XT. Did some prints last night and found that it did not want to stick to the plate at sharp angles, which i have to do, theres no way around it for my purposes. Im also getting constant bubbles at 240C, hotter makes it worse (0.2mm layers). The filament was just opened, less than 12 hours ago. Ive used both the recommended settings and my own on a Replicator 2. It ends up with big holes in the walls, and im using 3 shells….. Whats the problem here? Ive been an engineer for TechNation for a couple years now and ive never had this problem with our machines. I know to keep most filament it in silica jell, thats not the issue though because this is less than 24 hours old (since opening). Iv measure them in 6-12 different places and average it down to 3 decimals, in order to tune out the path lines that show up sometimes. It’s dead on…. I dont understand whats wrong but im about to send it back. Can you provide some insight or suggestions? Anyone? Im wondering, since the shrink wrap was pretty lacking compared to other filament providers, and because pink is not a popular color, perhaps it was sitting on a shelf for a couple years and now its soaked from humidity? Either way, im not putting a roll of it in the oven, i shouldn’t have to do that when i pay about $80 for one roll…. This needs to be on point and its not.
———- 2015/08/21 at 6:40 pm ———-
Oh i also need to note, yes, i use a heated platform and disappearing purple glue stick (one coat, dried). I also use brims up to 12-14mm… Sorry i would have edited but my “edit” button seems to be missing now. (that edit timer seems a little counter productive….)
———- 2015/08/22 at 12:12 am ———-
After further measurement, i found the filament, in the same spot (rotated) is from 1.66 to 1.71, and its all over the place all along the filament. I’ve tried adjusting flow and even averaging the oval out and it just wont print, ive tried heat from 235 to 260c at 35-50mm’s, with my closest measurements (im using a digital caliper), it skips at 50mm/s and makes bubbles (you can hear them popping randomly and frequently), even at 240c, which i think is the reason for the skipping, access pressure. After spending almost $80 for a roll of this, im a little upset.
Hi Kyle,
Please contact our support department for all these kind of issues: support@colorfabb.com
We will gladly work with you to resolve these issues and if this is indeed a bad spool, replace it.
Are there settings to make the resulting part watertight ? I am having some problems with leakage.
Watertight parts really depend on a good quality print where flow is always optimal.
Especially bottom layers can show leaking, so try and use plenty and make sure the first layer is nice and close to the bed.
Using 2 or 3 perimeter lines produce watertight parts no problem.
For specific questions, contact support@colorfabb.com
Your biggest enemy is flow. You need to over-extrude to get a square thread instead of a round one (this means you will have to slow it down a bit, you may also have to manually tweak speed for the bottom, as it will skip when making a flat surface easier than a wall). The round or oval threads create internal pathways for water. if one spot (in the hundreds of layers) isnt perfect and lets water through, it will fill the wall of that layer, and bleed from there. i recommend 3 shells to help ensure it melts all the layers (one extra pass) but be careful on overhangs; though 3 or more walls are good for overhangs, if theres a lot of detail on them, it will ripple, squish or break some of the outer shell lines in some cases. It depends how steep the wall gets and how detailed it is.
The other enemy is speed. You want to slow down a little bit and print hotter than normal to ensure every pass will make a uniform and solid bond, but be careful because slow speed will cause a more concentrated cone of heat (heat creep) and it can build up too much if its too slow, allowing the whole wall to warp badly, or the top layer to curl and get messed up that way too.
It becomes a balancing act.
Ive had no problem with the clear but with the pink, i get nothing but bubbles no matter what i do and if i make it too cold, it just skips if i dont slow it down, it just wont print. Im trying to get in contact with them right now and haven’t heard anything. Do you guys have any problems with their filament? Ive heard nothing but good things but after using it myself, i question if they were just noobs and not printing “real world” stuff. XT is a hybrid material, it behaves like ABS with little to no warping (dont get me wrong it will warp like anything else) but as far as water tight prints i recommend PET compounds. T-glase or PET+ work particularly well with liquid, thats what 2 liter bottles are made from. Same material with slightly different behavior for printing. XT will degrade with some solvents, but PET wont. I use it for shot glasses. Its also beautifully fiber optic. The red is particularly dazzling. Use thick, tall layers at slow speed and about 228-240c and it will look amazing. (cooler – more clarity, hotter-better bond and less warp) PET is a counter intuitive filament. It likes heat and slow speeds.
The filament is great, however need some advice on printing string free. I used XT Yellow and couldn’t get my print string free. I’m printing on an UM2 and used the following settings.
Layer height 0,06 mm and infill 20%
Temp 255ºC
Bed temperature 70º C
Speed 50 mm/s and reduced during the print to 40 mm/s
Retraction 4,5 mm
Retraction speed 150mm/s
Fans 100%
Flowrate 93% gives under extrusion and increased during print to 105% that worked fine
I didn’t have any issues sticking it to the bed I used a Brim and hairspray for that.
Any suggestions?
Hi Janet,
If you’re still having issues, please send this question to support@colorfabb.com with some more details about your printer, settings and possibly some pictures etc.
For XT on the Ultimaker 2 by the way 255ºC is quite high, especially when you’re extruding low volumes because of the small layer height.
I would suggest lowering the printing temperature to 240-245ºC
Hi all,
I did some really good prints with the colored XT material on a Makerbot 2X and I thought I’d share my findings with the community
I used these settings in Smplify3D (if you don’t know it it’s definitely worth checking out)
LayerHeight 0,25mm
4 top/Bottom layers – first layer at 90% height and 50% speed
2 shells
PrintTemp 240°
HeatedBed first layer 85° from the second one on 70° – this melts the material of the first layer into a nicely flat and shiny surface with almost no printlines
Cooling fan at 30% from the second layer – without cooling the walls literally collapse!
Printing speed 2400 mm/min
outline underspeed 50%
X/Y speed 9000 mm/min
Z speed 1200 mm/min
Extrusion multiplier is 1
Retraction 1,3mm
RetractionSpeed is 2700 mm/min
I’m really happy with the XT-color material and I can’t wait to see more colorvariations in the future.
.David
I’ve tried to print with the settings you’ve suggest, but the filament didn’t stick correctly. Can you tell me something more about the front and cover panels? During the printing process, did you left them opened or closed?
Moreover, I found that at 230°C, during the filament changing, it extrudes, but during the print process, it doesn’t’ extrude anymore.
Thanks,
Graziana
Hi Graziana,
_XT should have no problem sticking to a heated bed, especially with some glue stick.
Please make sure your cooling fan is off for the first layer and if possible a few layers more.
For our Makerbot Replicator 2 we have to print at around 240c as well so try to experiment with such a temperature.
It’s also possible you might need to go a bit higher, up to 250c should normally not be a problem for this material.
If you want some more specific support please contact us at: support@colorfabb.com with as much details you can share regarding the printer, settings and model etc.
Thanks,
Jos.
i print machine parts (mainly prototyping) on a flashforge dreamer. recently i start printing XT white. i print at 255 75 (no warping not even with big objects) at 40 – 50 speed. the only issue i have, is that i hear some clogging, but only during printing the infill. the perimeters / shells are printing just fine. does somebody know what is happening and what i can do about it
Check your slicer software for differences in your infill print speeds/parameters.
Change them to what works for the rest of the print (like perimeter parameters).
reslice the 3D model with the new settings and try printing it again.
Like Vizardknight mentions as well, check your infill speeds.
Also see if you can make sure that the infill is only put down in one direction in one layer. This way you will avoid crossings where the material can double up.
Lastly, we don’t have a Dreamer ourselves, but I think the temperature might be on the high side for printing with XT-Copolyester.
Hi, just received a spool of white XT and currently we’re not happy with it on our UM2…
The filament flows out the nozzle from the start of nozzle heating (from 200°C)… It looks like too liquid.
We’re printing a very complex model (anatomical model) with a lot of retractation actions (lots of support from cura) and there are a lot of strings (because some of the filament continues to flow during the movements of the nozzle).
Settings :
– 235°C
– 30mm/s
– fans 100%
– bed 70°C
– Flow rate 100%
We tried to print very slowly (20mm/s and add a lot of retractation like 6mm) but the results are nos as good as we expected.
Our old chinese 3mm PLA gave us best results…
Any ideas to help us ?
T
Hi Thomas,
Same UM2 printer.
I have minimized by increasing retraction lenght up to 7.0 mm and retraction speed to 45 mm/sec. Reduce temperature to 230 Deg C. I’ve pushed the flow to 110%. 100% speed. Almost string-free result.
On very complex model it can lead to slight under-extrusion but something to try!
Give me your e-mail address and I will share with you pictures.
Amitiés.
On my Craftbot I have found that there are blobs where it appears that the material is drooling out while in fast/non-extruding motion. I think this can be fixed using different retraction values. After trying several I still have them.
Currently, the best (but not that good) values I have are:
40mm/s speed
4.5mm length/distance
Any suggestions?
Thanks
Just built a spool holder for the colorfabb spools.. I really like them and transfer all my other filament to them.
http://www.thingiverse.com/thing:561092
hello
I bought a spool of clear XT last week. I’m printing with a Kentstrapper Volta (E3D V6 extruder)
I’m having some trouble with layer delamination.
I’ve printed a cylinder with tweak at Z plugin and setted steps of 5°C every 10 mm of print, from 265 to 245 °C (lh=0.2 mm speed=10 mm/sec fan off)
I saw good finish and better layer bonding at 265°C, but the print is still too much fragile.
Do I have to print at an higher temperature? Can I have some advice??
you and be both.. I cant get this stuff to work as advertized after two rolls.. same hot end.. and others. Higher the temps seems to make it brittle.. lower.. poor layer adheasion.. you really have to get the perfect temps to get it right.
What machine are you using Daniel? If you want we can assist you finding the settings. You can create a ticket at support.colorfabb.com
Hi Nicola,
10mm/s is probably to slow. The material is spending too much time in side the hot-end, which degrades the material. Try at 30-50 mm/s 0.2mm layer height temperature between 230-260C.
cheers,
Gijs
thank you for the useful advice!
meanwhile I’ve tried with 0.8 mm nozzle and little bit faster speed and the results were pretty good at 245 °C.
I think that your XT is an intresting material!
I love your blog
I have read this article and enjoyed it
Hello Community, this materials is Amazing! bridges comes out really nicely… but im getting a little bit warping.
using an U2,
75C bed temp
fill 0%
speed 30 mm/s
cooling fan 100%,
any suggestions?
thanks!
are these instructions taking intoconsideration the new color XT? and the new formula? I would really like an updated guide for those as I am having a terrrible time getting good prints from XT… too high temp and the prints come out brittle.. too low and they print clumpy..??
Some tips, for those that have other printer models without heated bed and do not have blue tape at hand: It is possible to make XT stick to glass (or probably anything) coated with PVA glue by squeezing the first layer on the bed (in my case layer height of 0.3 and width 300%) at very low printing speed.
Moreover, if you do not have a full metal hotend or for some other reason you cannot go too high with the temperature, it is possible to print with the XT even at 220°C, without particular layer bonding issues again by lowering the printing speed and keeping a considerable layer width.
(Tested with Smartrap http://www.smartrap.com/ and Genie hotend http://www.regpye.com.au/ )
This is just to encourage people that have different printers to try XT anyway since, believe me, this filament is really amazing!
Hi Cristian, thanks for sharing your insight! Very useful for those with other types of printer. XT is all about managing temperature en speed in order to get the amazing layer adhesion of this material!
Never heard about _XT before. Thanks for this review. I like neutral colors and it seems that the results are highly refined as I’ve seen in the images.
Here are some filaments reviews. Hope this helps. http://3dprinterblog.net/popular-3d-printing-filaments/
So, did you test with the other 3D printers? It would be nice to get some information on the various settings, as well as success stories.
The following printers are used in our lab:
Ultimaker Original
Ultimaker Original Dual Extrusion
Ultimaker 2
Makerbot Replicator 2s
Delta Tower (E3D hot-end)
Felix 20
Leapfrog Creator
Beethefirst
Hi Jeff,
It takes up a lot of time to do all the testing and documentation, which why we start with the most popular platforms such as Ultimaker and Makerbot. The other will follow as soon as we have some extra personal that will help out in our test lab.
Thank you for the tips, I am printing a electronics box for a friend and I wanted to see how transparent I could print the top cover so I could still see the leds on the board.
I created a 20x20x2 mm test piece and these are the settings that gave me the most transparent results:
Layer height: 0.1mm
Speed: 30mm/s
Fill: 100%
Temp: 220c (I have the “old” _XT that had to be printed between 220-240c)
Flow: 105%
No cooling fan.
What I learned was that for maximum top to bottom transparency you want to print slow with low layer heights, low temperatures, 100% fill and slightly more flow than normal but not too much. I print with a E3Dv5 hotend and 0.4mm nozzle.
Awesome filament 🙂
Hi Gert-Jan,
Thanks for sharing, great information that will be helpful for other users!
I love your filaments. I love the strength of the part when its made and I love the huge colour range. I would really love to try some 3mm in one of my huge printers. Are larger reels available? 20kg reels would be nice.
Cheers
Jason Simpson
Director
3D Group
http://www.3dg.com.au/
Hi jason, 20kg reels are not as standard available. If you’re really interested contact us at sales(at)colorfabb.com.
What percentage of flowrate should I use for best transparency? I was thinking of these settings on the Ultimaker 2:
lh:0.25mm
speed -40 mm/s
fill 100%
cooling fan off
250C nozzle temp
70C bed temp
retraction
40mm/s, 4.5mm retraction
flowrate: 107%??
Hi, those seem like pretty good settings. You might be able to print a little colder, maybe 240C.
I did a blog post here where I did a pretty nice transparency. Also I used 100% flow. That high flow rate above caused wasn’t good. It caused the beads(or whatever you call the individual extrusion lines) to look irregular and unclear.
http://www.jsquaredz.com/hell-skull-print-with-colorfabb-xt/
Hi, I found that increasing flow may help to get better transparency/gloss. I’ve pushed the flow up to 125%… Have you found the same?
250 C degrees works way better on Ultimaker 2 with 0.25 layer thickness…
Hi Bas,
Great will do some testing too! What speed are you using with these settings?
[…] Here are colorFabb’s advised printing settings with this material. […]
Awesome! thanks !
Thank you Sergey, hope the information is helpful.